When manufacturing LED lighting, LED binning is essential. This process determines the quality and performance of LED lights. But what exactly is LED binning, and how does it affect the LED lights you use daily?
LED binning is a method used to ensure the uniformity and grading of LED lighting products. It involves examining individual LED chips for their brightness, temperature, and other factors. And thus organize them into groups with similar features.
In this article, I will explain the concept of LED binning. You will also learn about the different types of binning. And how they impact the performance and efficiency of LED lights. So, let’s get started-
What is LED Binning?
LED binning is sorting and grouping LEDs based on their performance characteristics, such as color and brightness. Moreover, this ensures that each LED in a batch meets specific standards. And so you can use it in particular applications.
This process helps manufacturers and customers ensure that the LEDs they receive meet their requirements. Additionally, LED binning allows them to improve their production efficiency and quality.
Benefits of LED Binning
LED binning is essential to keep up the quality of LED lighting. And so it comes with many benefits, these are as follows-
Improved Color Consistency
LED binning allows manufacturers to sort LEDs by color and brightness. This ensures that all LEDs in a particular bin have similar properties. Thus, it improves the consistency of the final product.
Increased Efficiency
Manufacturers sort LEDs into bins based on their performance. For example, all its chips are tested to have equal power or brightness while manufacturing LED strips. If all the chips are not equally efficient, the output won’t be productive. All fixtures are tested in the LED binning process to maintain quality. And this increases the overall efficiency of the final product.
Better Quality Control
All fixture features are tested in LED binning, and non-standard components are eliminated. It also allows manufacturers to identify and address issues with their production process. Thus, LED binning improves the overall quality of the final product.
Types Of LED Binning
The sorting of LEDs is done based on a variety of considerations. Depending on this factor, you can group LED binning into Four main types. These are as follows-
Color Binning
Color binning is the process of sorting LEDs by their color characteristics. This ensures that all LEDs in a batch have the same color output and intensity. You can do this using advanced measuring equipment or visual inspection. Also, color binning helps guarantee consistent lighting performance.
- Importance Of Color Binning
It ensures the LEDs in a particular product have the same color temperature (CCT). Also, Color binning provides an accurate color rendering index (CRI). This makes the light of the LEDs consistent across all units. And the colors of objects are accurately represented.
- Standards for Color Binning
LED color binning is based on the CIE 1931 Chromaticity Diagram (from the International Commission on Illumination). This diagram has a series of quadrilaterals that identifies differences in light spectrums.
This CIE standard divides LED color temperatures into four categories. These are;
Type Of Color | Color Temperature (CCT) |
Warm | 2700K to 3500K |
Neutral | 3500K to 5000K |
Cool | 5000K to 7000K |
Ultra-cool | 7000K to 10000K |
The Color Rendering Index (CRI) and the Color Quality Scale (CQS) are the other standards used for LED color binning. The CRI measures how accurately a light source renders colors in natural sunlight. At the same time, the CQS calculates how accurately a light source displays subtle color differences. A good-quality LED must have a CRI of at least 80, whereas a CQS of at least 70.
- Methods for Achieving Consistent Color Binning
There are a few methods that can achieve consistent color binning in LEDs.
Spectrophotometry: This method involves measuring the spectral characteristics of each LED using a spectrophotometer. The data collected can then sort the LEDs into different bins. It is based on their color and brightness properties.
Colorimeter: A colorimeter is a device that measures the color of an LED by analyzing the light it emits. This information can sort the LEDs into different bins based on color properties.
Visual Inspection: This method involves visually inspecting each LED. It determines its color and brightness properties. Besides, this method can be less precise than the other methods. It is often used as a quick and easy way to sort LEDs into different bins.
Automated Binning: It is a process where LEDs are sorted into different bins using machine vision and robotics. This method is fast and efficient. However, it requires a high degree of precision. It also needs accuracy to produce consistent results.
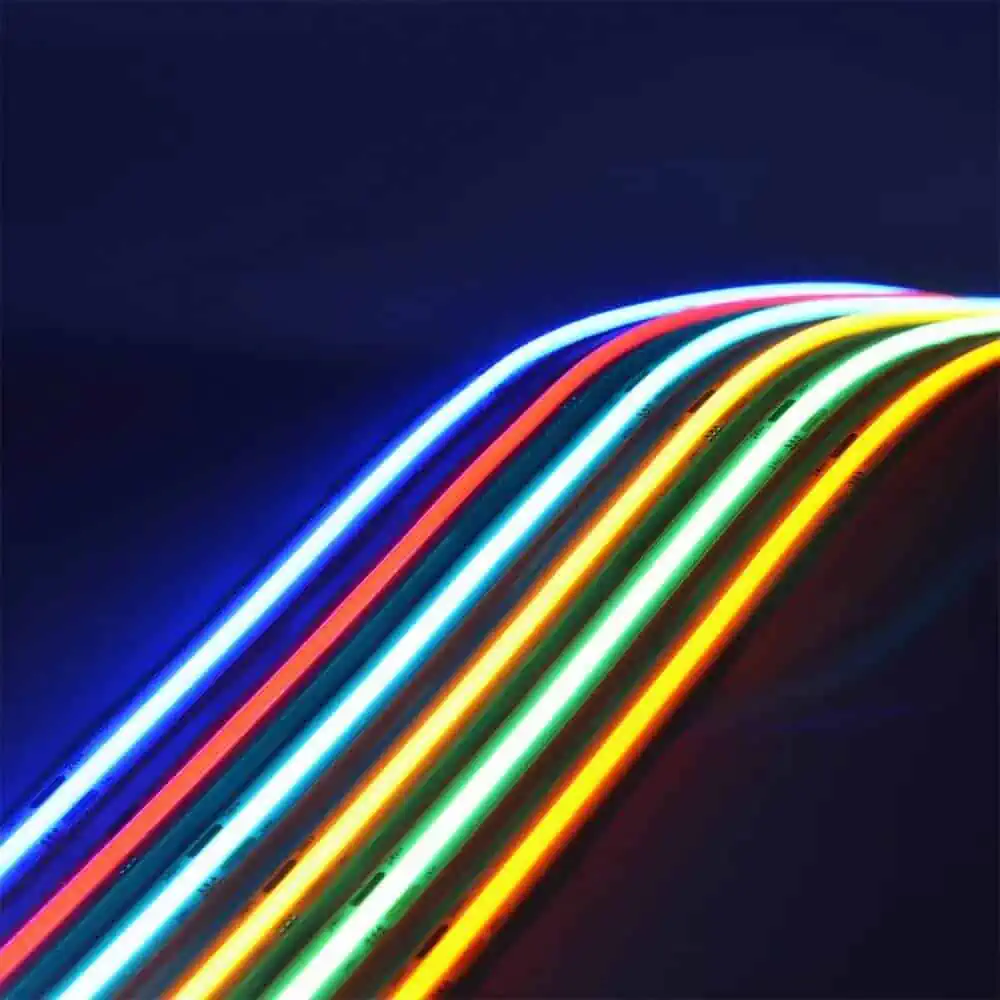
Luminous Flux Binning
Luminous Flux Binning categorizes LEDs into different bins based on their light output. The procedure entails counting each LED’s light output. After that, group them into bins based on brightness.
- Importance of Luminous Flux Binning
Luminous flux binning includes sorting LEDs based on the light’s brightness or output. Thus, it ensures all the fixtures in a batch glow equally bright. Also, it will produce consistent and uniform lighting. Besides, luminous flux binning eliminates the chances of using high-powered LEDs more than the requirements. And sorts the LEDs based on their brightness and efficiency. Thus, it reduces costs and increases profitability.
- Standards for Luminous Flux Binning
The luminous flux measurement determines the LEDs’ efficiency and performance. For each batch of LEDs, manufacturers set standards for acceptable luminous flux levels. These standards vary depending on the manufacturer. But generally, they include categories such as “A,” “B-grade, and “C.” “A” is the highest quality, and “C” is the lowest. For example, an A-grade LED might be expected to have a light output more splendid than or equal to 90 lumens per watt (lm/W). Besides, a C-grade LED might be expected to have less than 70 lm/W.
- Methods for Achieving Consistent Luminous Flux Binning
Several methods can achieve consistent luminous flux binning:
Statistical Binning: This method involves measuring the luminous flux of a large sample of LEDs. It divides them into groups based on their flux levels. This method is the most accurate and is commonly used in the industry.
Spectrophotometer Binning: This method involves using a spectrophotometer to measure the flux of each LED. However, this process of sorting is less accurate than statistical binning. Despite that, it is still widely used.
Visual Binning: In this method brightness of the LEDs is inspected visually. This method is the least accurate. Though, it is still commonly used in some applications.
Binning by Correlation: This method is a combination of statistical binning and spectrophotometer binning. The correlation between the two ways ensures binning consistency.
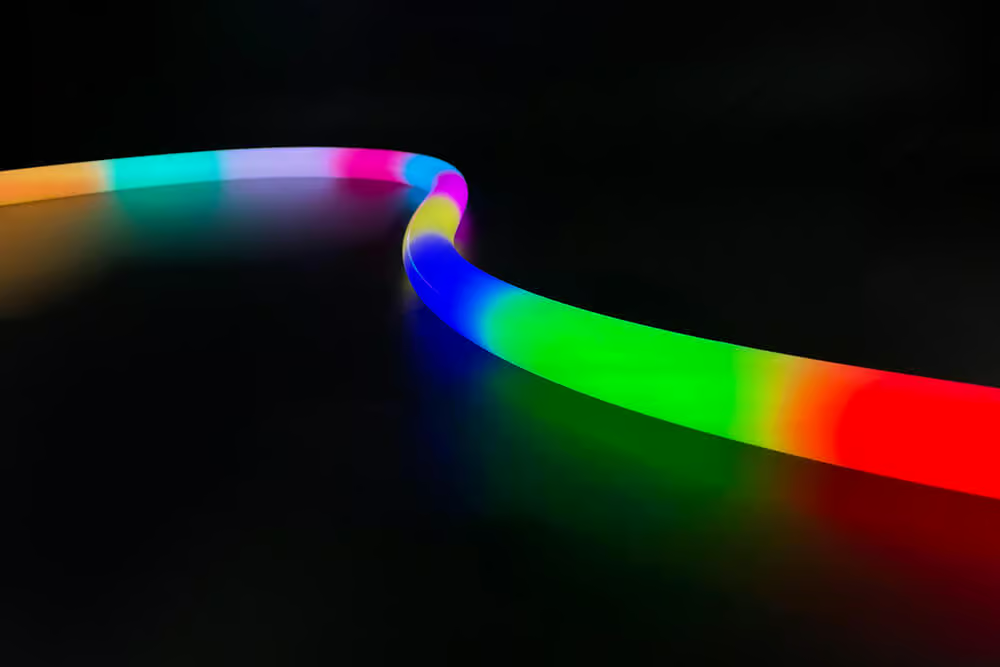
Voltage Binning
Voltage binning classifies LED components based on their voltage levels. This confirms that you can use them on the same circuit without risk of failure. The higher the voltage, the better the quality and performance of the LED component.
- Importance of Voltage Binning
Voltage binning tells whether the LEDs safety for use. It also ensures that it meets the desired performance standards. The voltage binning involves sorting LEDs into different “bins” according to their forward voltage. So you can identify LEDs with a higher or lower forward voltage than expected. It also allows you to sort out light fixtures that do not fulfill the standards. Thus, it reduces errors and improves the quality of the product.
- Standards for Voltage Binning
Based on forward voltage, LED bins are generally divided into four categories: high-voltage, low-voltage, standard-voltage, and ultra-low-voltage.
Forward Voltage Standard | Range |
High-Voltage | 4.0 – 4.2 V |
Standard-voltage | 3.3 – 3.6 V |
Low-voltage | 2.7 – 3.2 V |
Ultra-low-voltage | 2.7 V |
- Methods for Achieving Consistent Voltage Binning
Multi-sorting Method: This process involves sorting LEDs using multiple criteria. Such as voltage, current, and luminous flux. This ensures that the LEDs in each bin have a consistent voltage. Other characteristics will also result in compatible voltage binning.
Reverse Bias Method: This method involves applying a reverse bias voltage to the LED. And measuring the current flowing through it. LEDs with similar reverse bias current characteristics are grouped into the same bin. This ensures consistent voltage binning.
Temperature-Controlled Binning: This technique involves grouping the LED’s considering voltage characteristics at specific temperatures. Such sorting ensures consistent voltage binning across different temperature ranges.
Machine Learning-based Binning: This method uses machine learning algorithms. It groups LEDs into bins based on their voltage characteristics. Also, this ensures consistent voltage binning. It can also identify slight deviations in voltage that other methods may miss.
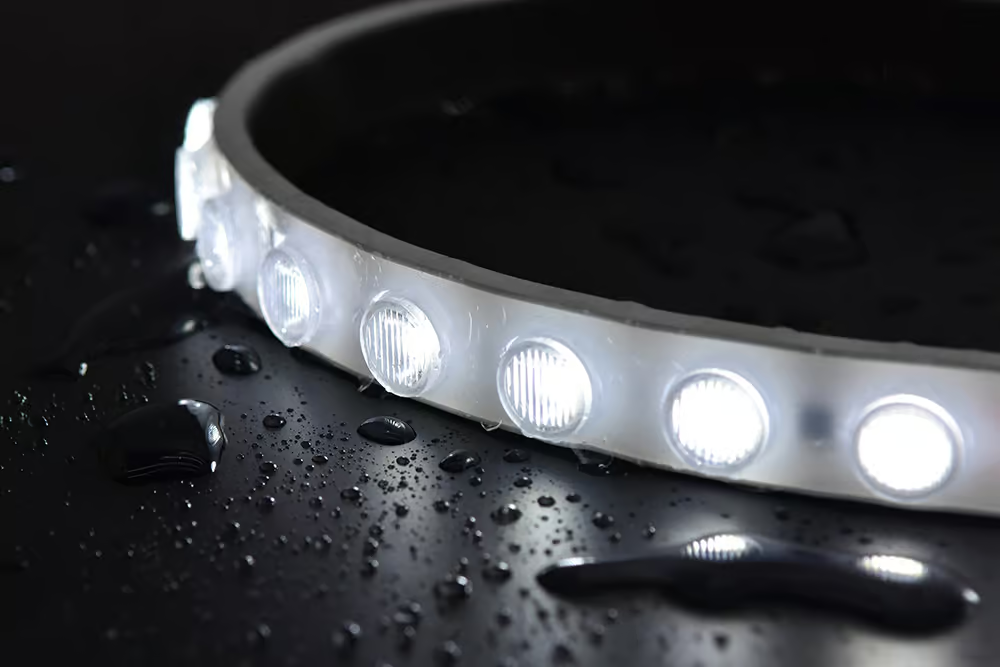
Temperature Binning
Temperature binning is sorting LED chips by their most operating temperature. Usually, LED binning is done at 25°C. But nowadays, a new system is implemented called hot binning. In this process, binning is conducted at a higher temperature (usually 85°C) than the traditional 25°C standard. Such binning improves the chromaticity selection and the consistency of the LEDs. However, the hot binning temperature varies with the LED fixture’s operating temperature.
- Importance of Temperature Binning
The performance of an LED can vary depending on the operating temperature. Some LEDs have to survive in the cold icing environment, while others are required to operate at higher temperatures. That is why temperature binning is essential to ensure the LED bins can conduct in the desired atmosphere. And so, hot binning is an excellent way to improve the temperature resistance of the LEDs. In this process, you must use a higher temperature for LED binning to ensure quality performance under unfavorable conditions.
- Standards for Temperature Binning
In LED binning, operating temperature is a significant factor that directly or indirectly affects the fixture’s lifespan. That is why temperature is considered while LED binning. Here is a chart that states the light’s operating temperature in different situations:
Different Lighting Cases | Operating temperature |
Outdoor Luminaires | 60° to 65°C |
Freezer Cases | 20° to 25°C |
Downlights in Insulated Ceilings/Retrofit bulb | often over 100°C |
So, while planning the LED binning process, consider the operating temperature. And calculate at which temperature you should test the LED chips to ensure their maximum performance.
- Methods for Achieving Consistent Temperature Binning
Calibration of Temperature Sensors: Temperature sensors need to calibrate. It ensures that they are reading at the correct temperature. The manufacturer can compare the sensor readings to a known temperature source, such as a thermocouple, and adjust the output.
Temperature Monitoring Software: Temperature monitoring software can track temperature readings and make adjustments as necessary. This software can also generate reports. They also alert the user when temperature readings are out of range.
Temperature Compensation Techniques: Temperature compensation techniques can correct temperature variations. These variations happen due to changes in ambient temperature. Besides, a thermistor can measure the ambient temperature. It can also adjust the power to the LEDs accordingly.
Thermal Management: Proper thermal management will help ensure consistent temperature binning. A manufacturer can do this by using heat sinks. Or they can use other cooling methods to dissipate heat generated by the LEDs.
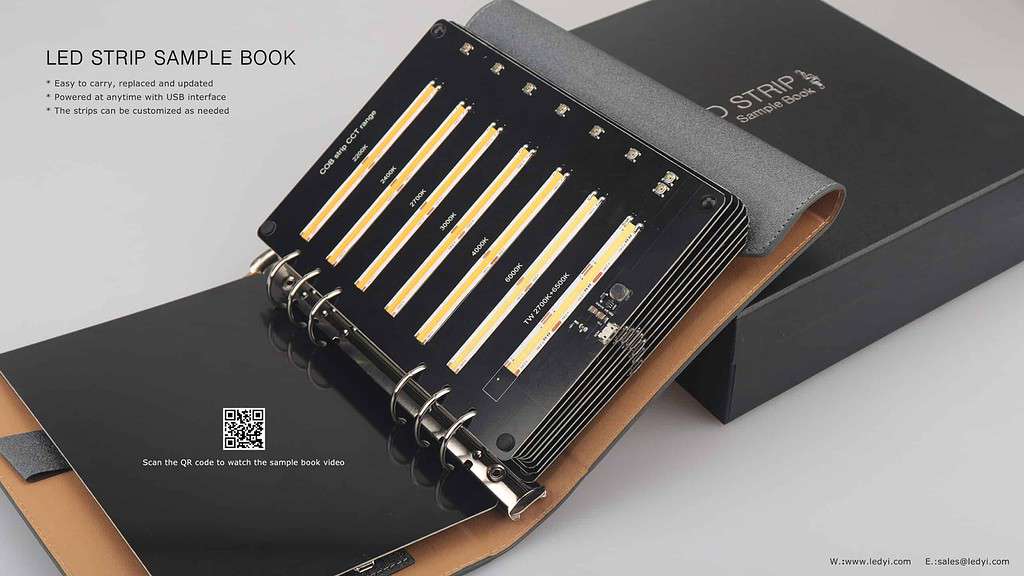
What is Macadam Ellipse?
Macadam Ellipse is a method used in LED binning to define the color variation of a group of LEDs. It is a graphical representation of the color coordinates (x, y) of a group of LEDs in the CIE 1931 color space. It measures the consistency of color across a group of LEDs. Also it calculates the distance between each LED’s color coordinates. It also figures the center of the ellipse. The smaller the ellipse, the more consistent the color of the LEDs in the group. This method is commonly used in the production of LED lighting products. It ensures that the LEDs are of consistent color and quality.
The Process of LED Binning
There are some essential steps required in LED binning. Let’s explore them below:
Step 1: Sorting LEDs by Voltage and Brightness
First, create an organized system of sorting based on the desired voltage and brightness levels. For example, you might use voltages ranging from 1V to 5V and brightness levels from 0 lumens to 500 lumens. Once your sorting system is in place, begin testing each LED individually. To do this, use a multimeter or other testing device to measure the current voltage. Also, measure the luminosity of each LED. After that, you can then place them into their respective bins.
Step 2: Slicing the Semiconductor into Die
In this step, you must slice the semiconductor with a diamond-tipped saw. Next, sort the die by color and brightness into bins. The sorting process is done with automated equipment. It can measure the light output of each die and categorize it according to the desired standard.
Step 3: Wire Bonds and Electrical Connections
Wire bonds create a tight electrical connection by wrapping the metal strand around cables. This process ensures that the connection is secure and reliable. Once the wire bonds are complete, you must attach the LED components to their power source using solder or crimp connectors. Now, your LEDs are ready to sort.
Step 4: LED Binning
After ensuring proper wire bonds, sort the LEDs according to specific criteria. Consider the size, color, voltage, and other factors and group them accordingly. First, measure the light output of the LEDs using a lux meter. This ensures that the brightness level meets the desired specifications. Then, they use a spectrometer to measure each batch’s color accuracy and consistency. Also, check the size of the chip and its voltage. In this process, automated machinery is of great help. Besides, these can also be done manually but won’t be reliable.
Step 5: LED Quality Control
After LED binning, it’s time for a quality test. Here the QC team looks for potential defects, durability, and other tests. And thus, verify that each batch meets its quality standards with these tests.
Thus following these simple steps, you can successfully carry out the LED binning process.
What is the Difference Between Color Binning and Flux Binning?
Color binning and flux binning are two methods. They sort and classify lights based on color and brightness.
Color binning involves sorting and classifying based on light’s coloring properties. It can be the range of wavelengths of light that they are most sensitive to. This is typically done by measuring the device’s spectral response. And then group them into different “bins” based on their characteristics.
Flux binning, on the other hand, involves sorting LEDs based on lumen ratings. In this process, LEDs are grouped by their brightness. The higher the lumen rating, the brighter the light.
To sum up, color binding deals with the coloring properties of light. Meanwhile, flux binding considers the brightness of the light for LED sorting.
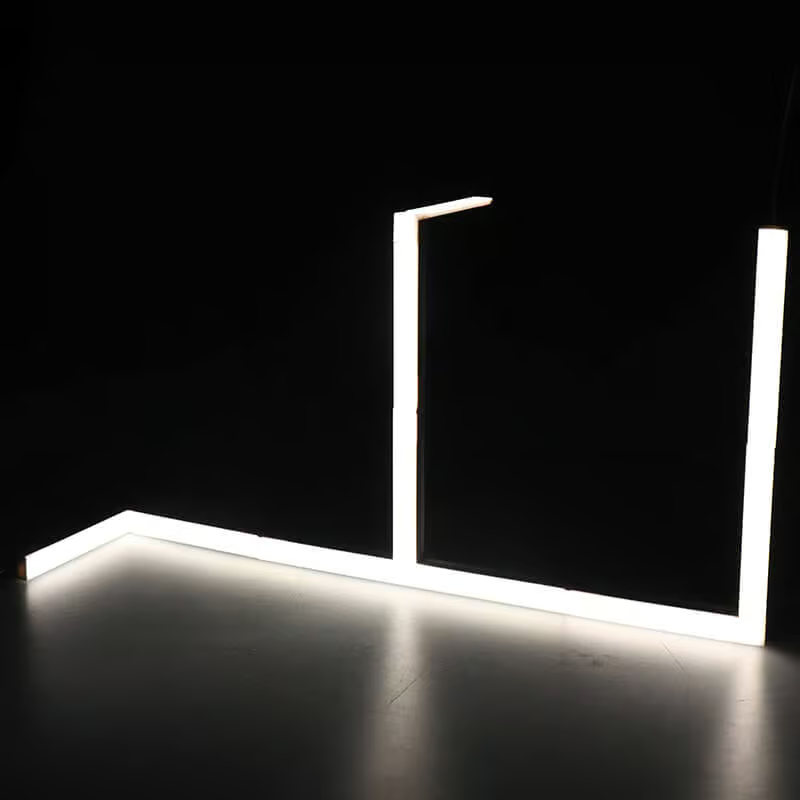
Factors To Consider While LED Binning
Several factors can affect the success of LED binning:
Bin Criteria
In LED binning, you should consider the following bin criteria:
- Luminous Flux: The light emitted by the LED is measured in lumens. LEDs are grouped into bins based on their luminous flux. Higher bins have higher flux levels.
- Color Temperature: The color of light emitted by the LED, measured in Kelvins. LEDs are grouped into bins based on their color temperature (CCT ratings). Higher CCT bins have cooler (bluer) colors, and lower ones have warmer (redder) colors.
- Forward Voltage: The voltage required to drive the LED, measured in volts. LEDs are grouped into bins based on their forward voltage. Higher bins have higher voltage requirements.
Technology Considerations
Technology considerations for LED binning include:
- Measuring Equipment: Accurate measuring equipment is necessary to test. It is also vital to sort the LEDs based on their performance characteristics.
- Binning Algorithm: The algorithm to sort and group the LEDs should be consistent and repeatable.
- Temperature: This can significantly impact the performance of LEDs. So, measure and bin the LEDs at a consistent temperature.
- Binning Standards: Different applications may require different binning standards. Understand and adhere to the appropriate binning standards for a given application.
- Automation: Automated binning systems can increase efficiency and reduce human error.
- Traceability: It is important to be able to trace the binning process. Also, trace the characteristics of each binned LED.
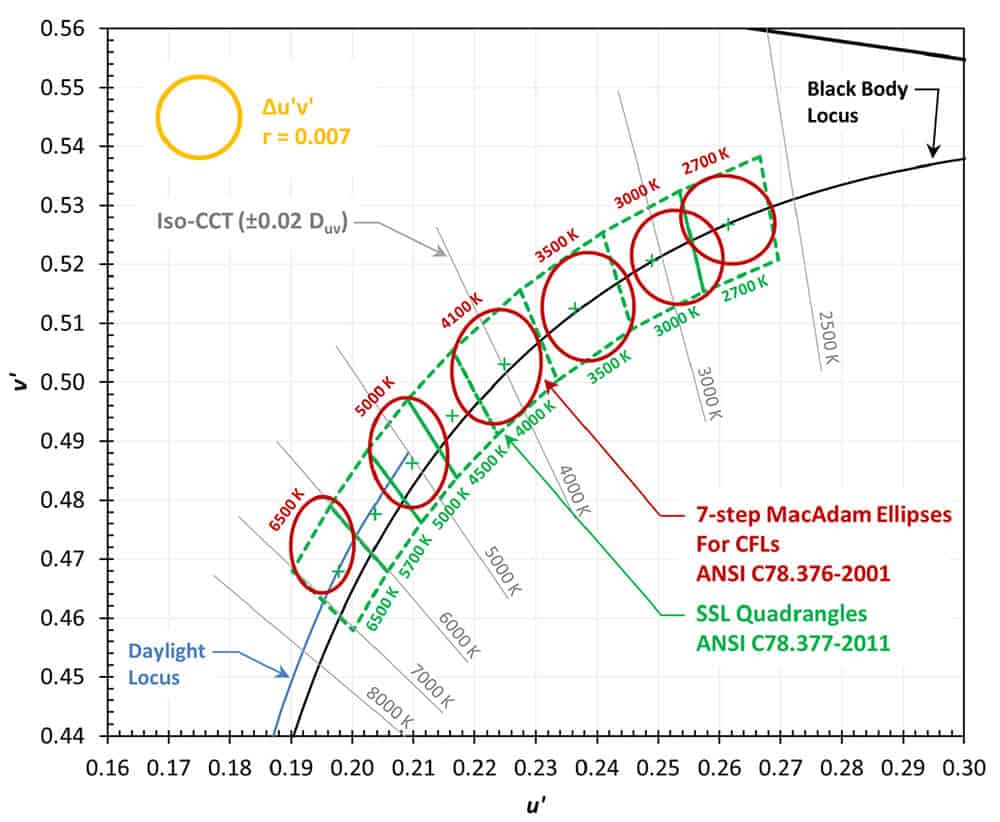
Industry Standards for LED Binning
Industry standards for LED binning vary depending on the applications. Some common standards have:
- ANSI C78.377-2017: The American National Standards Institute (ANSI) developed these criteria for LED lamps and luminaires. It defines the color and chromatic specifications for general lighting services.
- IES LM-80-08: The Illuminating Engineering Society (IES) developed this standard. They give guidelines for measuring and reporting the lumen maintenance of LED light sources.
- JEDEC JS709A: The Joint Electron Device Engineering Council (JEDEC) developed this standard. They define the binning and sorting needs for high-brightness LEDs.
- CIE S025/E:2017: The International Commission on Illumination (CIE) set this standard. They provide guidelines for the color coordinates of LED light sources.
- IEC 60081: This standard is for fluorescent lamps. It defines 5-step MacAdam ellipses for six nominal CCTs.
Environmental Regulations for LED Binning
Environmental regulations for LED binning vary by region and application. But some standard conditions include;
- Compliance with RoHS (Restriction of Hazardous Substances) Directive: This EU directive bans using certain hazardous substances in electronic products. They include lead, cadmium, and mercury. So, while LED binning, you must consider this fact.
- Energy Efficiency Standards: Many countries have energy efficiency criteria for lighting products, including LED products. These standards may specify minor energy efficiency levels. Also, it can be the maximum power consumption level for other types of products.
- Safety standards: LED products must follow relevant safety standards. Such as UL and CE. This ensures that they do not pose a fire or electrical hazard.
These general guidelines and regulations may vary in different countries and regions. Manufacturers should be aware of the rules while LED binning.
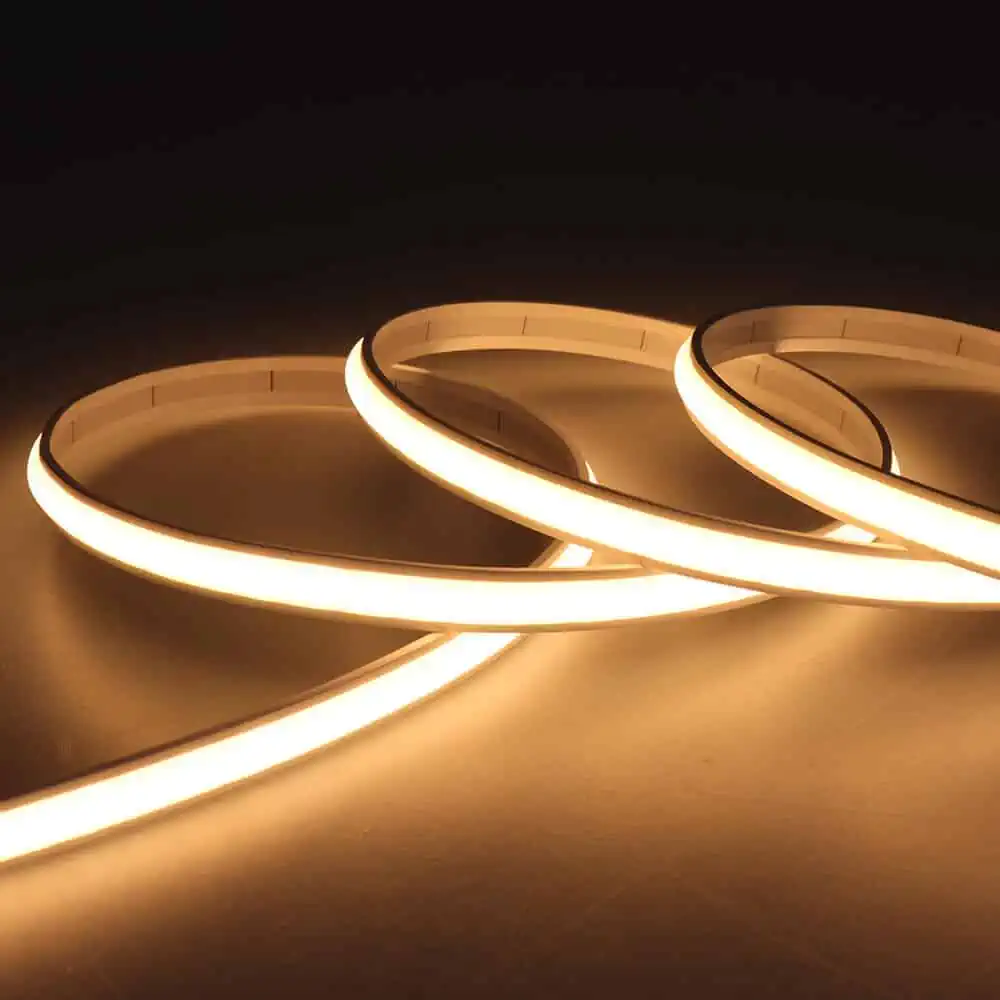
Thermal Effects of LED Binning
The thermal effect on LED is inversely proportional to the forward voltage, VF. When the temperature increases, the forward voltage drops, increasing the current flow in the LEDs. And excessive current flow can negatively affect the performance of the fixture.
Another thermal effect of LED binning is the impact on the luminous flux of the LED. The luminous flux of an LED is affected by the temperature of the LED. As the temperature increases, the luminous flux decreases. And thus, it directly affects the brightness of the lighting.
In addition, thermal management can also affect the overall lifespan of an LED. As an LED’s temperature increases, the LED’s rate of deterioration also increases. It leads to a shorter lifespan. Proper thermal management can help to mitigate this effect.
Common Issues or Challenges with LED Binning
While LED binning, you may face some common issues, which include:
- Color Variations: In the LED binning process, the sorting and grouping of LEDs are done, keeping the coloring feature of all bins constant. Yet, some LEDs may have slight variations in color. They can affect the appearance of a lighting system.
- Lumen Depreciation: LED binning also sorts LEDs by their luminous flux and brightness. Yet, over time, an LED’s brightness can decrease, which is known as lumen depreciation. This can cause uneven lighting and affect the performance of the system.
- Incorrect Binning: If LEDs are not correctly sorted or grouped during the binning process. It can lead to a mismatch in performance and color. This can cause issues with the lighting system.
- Cost: Binning LEDs can be a costly process. It requires specialized equipment and skilled personnel. So, this can affect the overall cost of a lighting system.
How to Test a Binned LED?
To test the binned LED, you need to follow these steps:
Step 1: Connect the LED to a Power Source: Attach the LED’s positive lead to the power source’s positive terminal. Then touching the negative charges to the negative terminal. And thus examine if the LED glows or not.
Step 2: Measure the Voltage and Current: Use a multimeter to measure the voltage across the LED and the current flowing through it.
Step 3:Calculate the Value of the Resistor: Use Ohm’s law to calculate the value of the resistor. The formula is R = (Vsource – Vf) / If
Step 4: Compare the Readings with the Specifications: Check the datasheet of the LED to see what the expected voltage and current should be for that binned LED. Compare the readings from the multimeter with the specifications.
Step 5: Observe the Light Output: If the voltage and current readings match the specifications, observe the light output of the LED. If it is not as expected, there might be a problem with the LED.
Step 6: Repeat the Test with Different Power Sources: Repeat the test with different power sources to ensure the LED functions correctly.
Note: Binned LEDs are categorized based on their forward voltage and current. It is essential to test these values to ensure that the LED is functioning correctly.
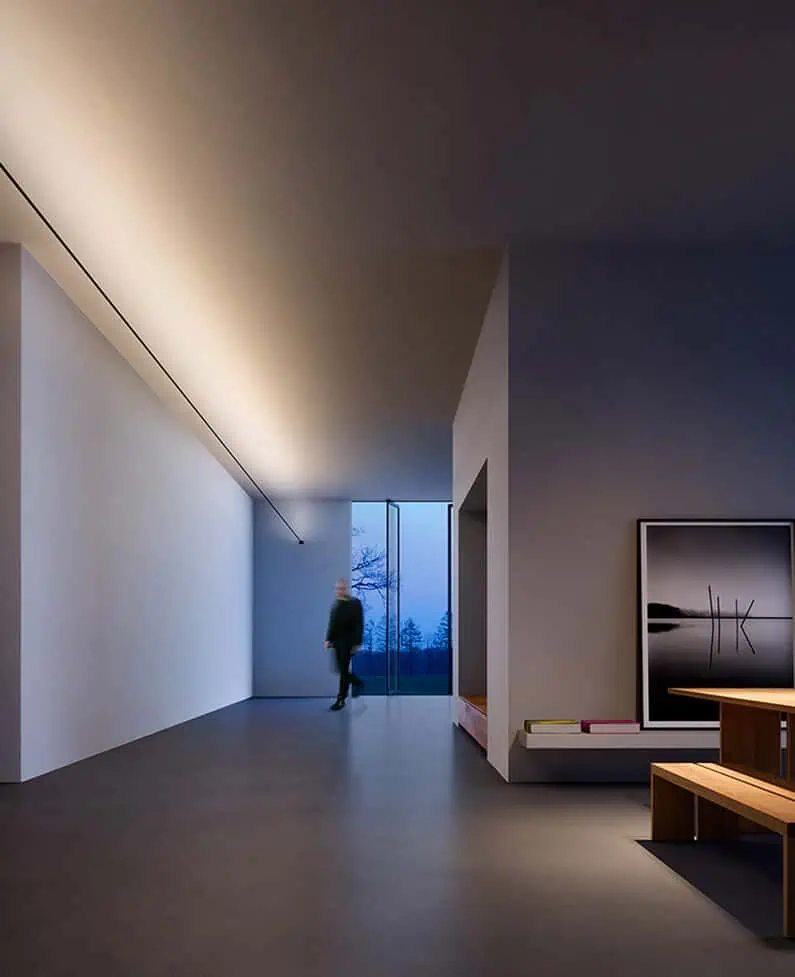
Tips for Optimizing Your LED Binning Process
- Clearly define your desired LED binning parameters: Identify the parameters you wish to use for binning. Such as color temperature, luminous flux, and forward voltage. This will ensure that all LEDs are evaluated against the same criteria.
- Use a consistent testing methodology: Use consistent testing methods throughout the binning process. This may include using the same tools and measurement techniques, also, testing conditions for each LED.
- Use automated binning software: Automated binning software can streamline the binning process. Also, it can reduce the potential for human error. These programs can automatically sort LEDs into different bins.
- Keep detailed records: Keeping detailed records can help troubleshoot any issues that may arise. As well for future reference. This may include information about the testing equipment used. Also, the binning parameters and the results of each test.
- Regularly review and adjust your binning process: Reviewing and updating your binning process can ensure you always get the best results. And it will solve the previous problems.
Consider the final application: This will help you identify essential binning parameters. It ensures that you select the best LEDs for the specific application.
FAQs
LED Bin codes typically consist of 3/4 characters or letters. This code indicates an LED’s flux, color temperature, and forward voltage. So, with a bin code, you can know the standard features or get an idea about the LED output.
Yes, there are industry standards for LED binning. The Illuminating Engineering Society (IES) establishes these standards. This standard includes some aspects like- luminous flux, CCT, etc. Additionally, some manufacturers have their proprietary standards to meet precise needs.
Yes, LED binning can be done after the manufacturing process. Yet, it is best to do this before to ensure correct LED sorting. Binning after the manufacturing process can result in a lower-quality product. This could be due to a potential mismatch between the bins and the individual LEDs.
Binning affects color consistency because different bins may have different colors. Even though they are marketed in the same color, the color of LED lights from different bins may not match. This will cause inconsistencies in the final lighting effect.
LED binning is not necessary for all types of LED lights. But it is commonly used for applications where consistent color is essential. It is particularly true for lighting projects that require uniform color. Such as in commercial or architectural lighting. Yet, where color consistency is not as critical, LED binning may not be necessary.
Standard binning tolerance is measured in color temperature, chromaticity, and luminosity. For example, a typical binning tolerance for color temperature could be within ±100K. Chromaticity tolerance could be within ±0.005 on the CIE 1931 chromaticity diagram. Also, the luminosity tolerance could be within ±5% of the specified brightness level. These tolerances vary depending on the manufacturer and the application.
Yes, LED binning can lead to higher production costs due to the sorting and grouping process.
If LED lights are not correctly binned, it can impact the dimming capabilities of the lights. If the LED lights have different brightness levels, it will result in uneven dimming. It can also have a less desirable lighting effect. Proper binning ensures that all LED lights have the same brightness and color quality. This results in a smoother and more consistent dimming experience.
Conclusion
In conclusion, LED binning is a sorting process of LEDs. It organizes LEDs based on their optical and electrical characteristics. This process allows manufacturers to confirm that they package LEDs with similar features. And thus, LED binning improves the performance and character of LED-based products. It will continue to play a tremendous role in the development and advancement of LED technology.
LEDYi manufactures high-quality LED strips and LED neon flex. All of our products go through high-tech laboratories to ensure the utmost quality. Besides, we offer customizable options on our LED strips and neon flex. So, for premium LED strip and LED neon flex, contact LEDYi ASAP!